While learning how to machine using the lathe and mill, I became interested in what seemed to me a chicken/egg problem; “How do you make a precision instrument if you don’t have a precision instrument to make it with?” The answer: it starts with a flat surface, and you build up from there. (For more about this answer, I recommend “Foundations of Mechanical Accuracy” by Wayne Moore.)
Precision starts with a flat plane. Without a smooth, regular surface, it would be nearly impossible to create square objects, and from there, impossible to build all the machines and technologies to create the world around us. (Also, I can’t help but mention that as I wrote this, I was reminded of the flat plane of Central Place Theory by Christaller, for the geography nerds out there.)
And thus my unhealthy obsession with flatness began.
I started with reading about Surface plates, the granite plates that have been ground to millionths of an inch flatness. A typical surface plate you may see in a shop would be 24″ by 36″ and 4″ thick, cut from granite and ground flat with diamonds. (For a very bad copy of the Federal Specification from the GSA, which almost all surface plate manufacturers base their tolerances on, because you can’t easily find the new spec, see here: the older spec, GGG-P-463c, now superseded by ASME B89.3.7.) In order to meet these standards, you need to have your surface plate calibrated, so how do we go about doing that?
And this is where I came across the weird looking thing, with the name straight from the 1950’s: the Rahn Repeat-O-Meter.
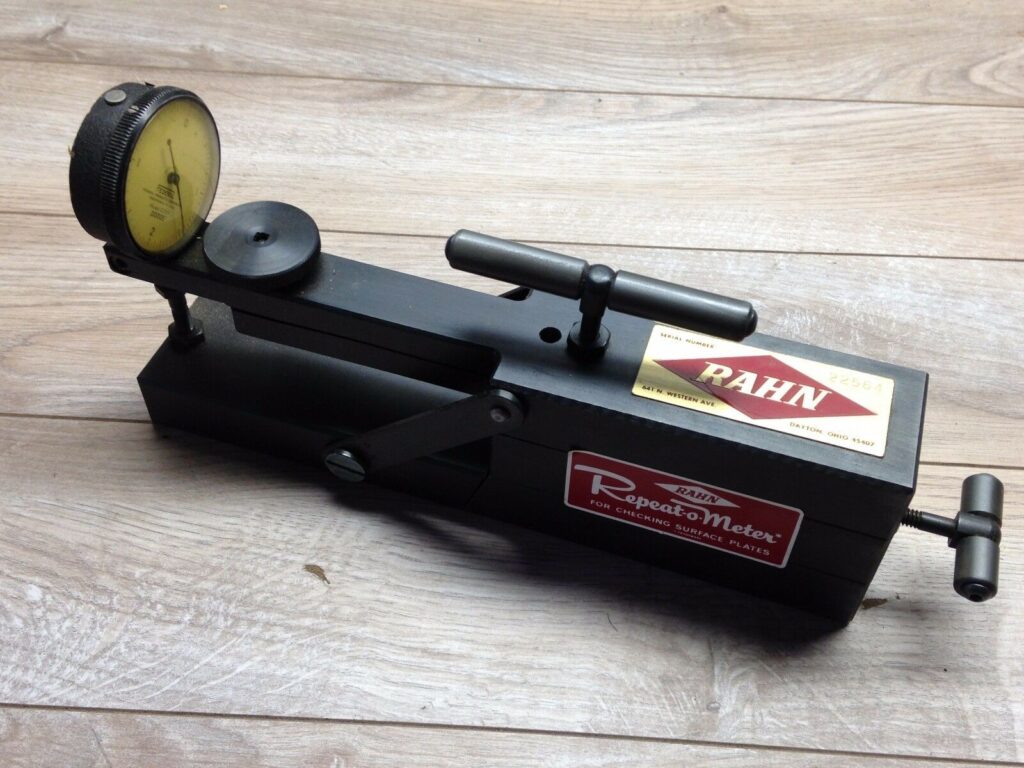
A Repeat-O-Meter measures the variation in relative flatness across the surface plate. It’s a rather simple device, consisting of essentially a floating lever attached to a base. The base has an arm above the lever that holds a high precision dial indicator (0.00002″usually.) The lever lifts the plunger on the dial indicator as you sweep the whole thing across your surface plate. And as you move the Repeat-O-Meter around your plate, you see the variation in the flatness of your plate (relative, because it shows the variance from one point on the plate compared to another point.) Obviously, the less variance, the better the plate for high precision work.
When I googled the Repeat-O-Meter, I came across one of my favorite machinist Youtube Channels, Oxtoolco (Tom Lipton) and his videos on the Repeat-O-Meter and re-surfacing his granite plates, and his collaboration with NYCCNC on re-creating their own DIY Repeat-O-Meter. (And by the way, you’re going to see a lot of references to Tom Lipton on this blog when it comes to metrology, flatness, and all things machining. He’s my spirit animal.) And just as an aside, I’d be remiss not to mention this amazing design by Robin Renzetti.)
However, my biggest influence was the guys at Bar Z. This video (and their blueprints found in the description of the video) of their own DIY mini Repeat-O-Meter.
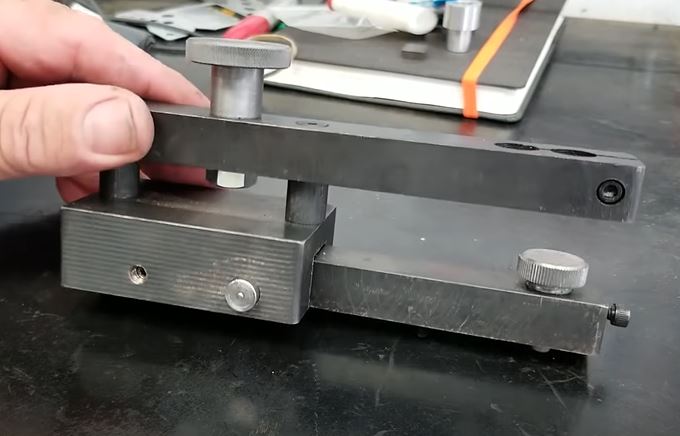
Now, I didn’t learn all this all at once. I had been reading and watching these videos over a period of a few months. And in that time, I had enough use for a surface plate that I bought a small (12″ x 8″) import granite surface plate from Ebay. And not knowing how flat this rather inexpensive and small plate was, I wanted a wear to investigate it’s properties. So I set out to make my own Repeat-O-Meter.
And this is where the trouble began….
(Next Up: “A slight change.”)